Tips of Low volume Manufacturing by CNC Milling
Low volume manufacturing using CNC milling can be an efficient and cost-effective way to produce small batches of parts. Here are some tips to optimize the process:
1. Design for manufacturability:
- Simplify geometries where possible
- Avoid deep pockets and narrow channels
- Use standard tool sizes and radii
2. Material selection:
- Choose materials that are easy to machine (e.g., aluminum, brass, plastics)
- Consider using pre-cut stock to reduce material waste
3. Tooling optimization:
- Use high-quality cutting tools appropriate for the material
- Minimize tool changes by using common tool sizes across parts
4. Fixturing and workholding:
- Design simple, reusable fixtures
- Use modular workholding systems for flexibility
5. CAM programming:
- Optimize tool paths to reduce cycle times
- Use adaptive clearing strategies for efficient material removal
- Simulate programs to catch errors before machining
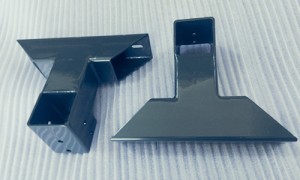
6. Machine setup:
- Create standardized setup procedures
- Use quick-change tooling and workholding systems
7. Batch processing:
- Group similar parts together to minimize setup changes
- Use multi-part fixtures when possible
8. Quality control:
- Implement in-process inspection to catch errors early
- Use coordinate measuring machines (CMMs) for critical dimensions
9. Finishing:
- Consider post-processing requirements (e.g., deburring, surface finishing)
- Automate finishing processes where possible
10. Documentation:
- Create detailed work instructions and setup sheets
- Document best practices and lessons learned for future runs
11. Automation:
- Consider using a pallet system for unattended operation
- Implement robotic loading/unloading for longer production runs
12. Continuous improvement:
- Analyze cycle times and look for opportunities to optimize
- Gather feedback from operators and implement improvements
By following these tips, you can improve efficiency, reduce costs, and maintain high quality in low volume CNC milling production.